Compressed Air Systems
Extensive experience with design of low pressure, medium pressure and high pressure compressed air systems.
Extensive experience with installation design for reciprocating, rotary screw and centrifugal air compressor systems; lubricated and oil free.
Responsible for the design of approximately 50% of the 600 psi centrifugal compressor installations for the PET industry in North America.
Typical capital and operating cost savings initiatives:
- Design of compressor rooms to optimize compressor efficiency through temperature control and humidity control.
- Design of compressor installations to optimize condensate removal; air-saver condensate removal traps, condensate buffer systems to prevent a wet environment, etc.
- Use of closed loop compressor cooling systems with low dissolved and suspended solids to prevent expensive fouling of high temperature compressor heat exchangers.
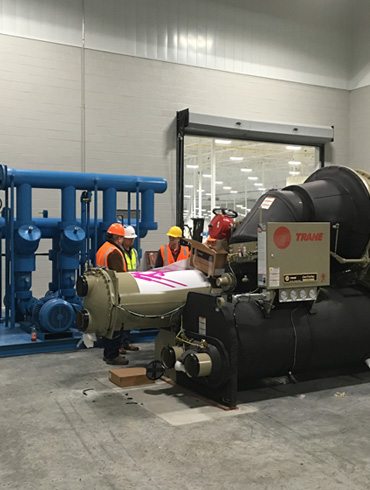
Chiller Plants
Extensive experience in both Ammonia and HCFC Systems.
Design and implementation of high efficiency central filtration systems and water treatment systems in addition to point of use filtration.
Process equipment life and process stability are optimized due to minimal deposition of dissolved and suspended solids.
Customized systems design to match plant process and HVAC requirements.
Typical capital and operating cost savings initiatives;
- Design of central closed loop systems using high efficiency centrifugal air separation systems. Pumping efficiency is optimized while avoiding typical issues with air removal.
- Design of low temperature, low pressure, low flow central pumping systems with point of use VFD bridle loop pumping systems to control process specific flow and temperature.
- Energy efficiency is optimized by utilizing only as much horsepower as is required by specific processes through bridle loop pumping design.
- Process control is optimized by point of use control of temperature and pressure.
- Design of primary variable pumping systems for central chilled water pumping systems.
- Reduced capital costs and power consumption due to elimination of constant flow chiller supply pumps.
- Assistance with development of high efficiency centrifugal ammonia chiller systems.
Water Cooling and Boiler Systems
Three dimensional structural and piping design
- Eliminates contractor bid padding that is required for vague bid packages and/or for design-build bids.
- Pre-fabrication of structures and piping reduces costs and accelerates project schedules.
- System interferences are avoided due to integration with three dimensional drawings of equipment, duct work and electrical services.
- Change orders are minimized due to avoidance of interferences and due to minimal field design modifications.
Integrated chiller plant, HVAC systems, cooling tower systems design, boiler systems, and water treatment systems. Pumping and piping system costs are minimized due to comprehensive facility design approach.
Design and specification of central automation controls and HMI’s for integration of all utility and HVAC systems. Energy efficiency is optimized. Supervisory controls and troubleshooting tools are centralized for ease of operation and for maximum process stability.
Detailed equipment and contractor bid packages result in high quality equipment and installation at competitive pricing.
Customized systems design to match local conditions and process requirements. Strict avoidance of “cookie-cutter” utility systems designs that do not optimize energy efficiency and process stability based upon local climatic conditions and/or plant-specific requirements.
Sample capital and operating cost savings initiatives;-Recovery of HVAC condensate water reduces make-up water costs and chemical treatment costs.
- Free heating of incoming city water and free cooling of tower water for process supply.
- Design of energy saving closed loop cooling systems without typical issues with air removal or system capacitance.
- Isolation of scale-sensitive equipment from open loop evaporative cooling tower water.
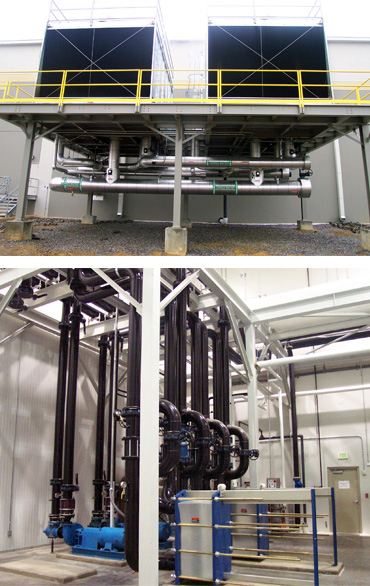
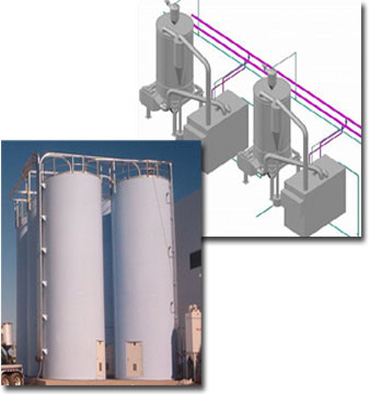
Material Handling Systems
Extensive experience in plastic resin handling systems; silos, volumetric blending system, gravimetric systems, vacuum pumping systems, mass flow conveying systems, rail car unloading, truck loading and unloading, storage systems, etc. More than 600 million pounds per year of resin handling systems installed during the last five years.
Extensive experience in resin and material drying systems including electric and gas fired systems, desiccant drying systems, infrared drying systems, adiabatic drying systems, etc.
Design experience in scrap and post-consumer material recovery, cleaning, granulation, recycling and re-processing systems.
Extensive experience with in-plant scrap recovery systems, scrap conveyance and scrap blending with primary material stream.
Design experience with replacement of batch and batch blending systems with continuous stream digital blending systems for both dry and liquid blending systems for beverages, resin handling systems and other applications.
Generation of bid specifications and sequence of operation for vendor supplied material handling and control systems.
HVAC Systems
Three dimensional equipment, duct work, structural and piping design.
- Process specific air flow design to optimize distribution without impacting temperature sensitive processes.
- Process specific duct work and diffuser design to preferentially control dew point in humidity sensitive areas.
Extensive experience in central building controls systems using Allen Bradley, Trane Tracer, etc.
Integration of ventilation, air conditioning, dehumidification and heating systems and overall facility air balance.
Customized systems design to match local conditions and energy costs. Detailed evaluation of capital and operating cost comparisons of DX systems versus chilled water, ventilation vs. air conditioning, electric, gas or boiler system heating, passive ventilation supply vs. forced air supply, etc.
Typical capital and operating cost savings initiatives;
- Utilization of chilled water HVAC where chiller plant is otherwise required for process (see chilled water plant initiatives).
- Evaluation of return on investment on compressor room air conditioning/dehumidification for large air compressor plants and implementation where justified.
- Design of displacement ventilation systems for reduction of air conditioning loads in production rooms through vertical stratification of temperature zones.